Engineering and maintenance: the outsourcing question
October 1999
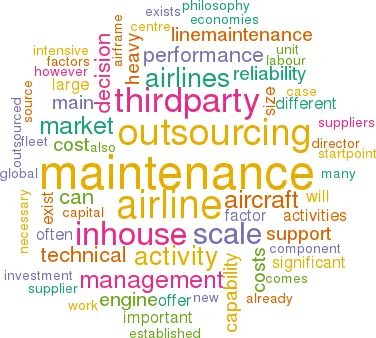
In Engineering and Maintenance (E&M) management, there are multiple questions to consider. What E&M activities should be outsourced, if any? Should existing E&M activity be a profit centre, a subsidiary or just sold off? On what basis should E&M suppliers be selected? How can the maintenance contract ensure performance and service standards (for both in–house and external supply)? What performance standards should be measured and incentivised, and how?
In this article Aviation Strategy reviews the question of outsourcing, and in upcoming issues we will look at organisation and contracts, then at supplier selection and performance measurement. The first observation is that there is no one, global right answer. Actual airline practices show a vast number of approaches, adopting different models for some or all of their maintenance activity (see table below).
Key factors
There are four main factors that impact the ultimate outsourcing decision for an airline:
1. The start-point. Start–up airlines with no resources operate in a very different environment from established carriers which have been doing maintenance for many years, and which frequently have a role as an important national employer with strong union representation. The other relevant start–point is the extent to which E&M is genuinely a source of advantage to the airline. For example, for Lufthansa, the quality of its E&M has created — in the customers view — with a halo effect of reliability and safety. However, its capability also offers hard cost advantages — e.g. those derived from build–quality on engine overhaul.
2. Competitive third-party market. Many airlines developed in–house capability at a time when there was no alternative available. Today, in virtually all areas of E&M, there is a viable and contested third–party market.
In engine and component support, the manufacturers (OEMs) have recognised after–market support as a source of long–term, and higher, margins, and have entered the market vigorously. With their financial muscle and global reach, companies like GE and AlliedSignal have successfully established a strong market presence. Large airline third–party shops offer size, operating experience, incremental pricing and global access. Independent suppliers still exist but face tough challenges from competitors with significant advantages.
In heavy airframe maintenance, the major OEMs do not today participate as actively, though Boeing has considered the idea. The major players are again the airline third–party shops and a few notable independents who have gained the scale and business base to succeed (e.g. Tramco, FLS Aerospace).
The main line–maintenance decision is what to do at the main base(s). Assuming that most airline hubs will be at reasonably sized airports, then it is likely that a third–party alternative exists. If not, then line capability has to be established. Down–route, line–maintenance cover is often outsourced.
3. Economies of scale. Economies of scale do exist in E&M. Heavy airframe maintenance is labour and capital (hangar, tooling) intensive. Engine and component support are very capital intensive, with the former also requiring high–tech capabilities. Scale can also offer benefits in line maintenance due to its 24–hour nature, shift systems, minimum staffing requirements and peaks and troughs in activity associated with banks of aircraft movements.
Where is the cut–over point at which it makes sense to develop in–house capabilities? Clearly the maths varies by carrier and region, but a common view is that a fleet of over 50 aircraft or more than 150 engines is normally required to justify in–house heavy maintenance capability. Airlines below this threshold should consider either joining with others to create a heavy maintenance operation of the necessary scale or outsourcing maintenance to a large cost–effective third–party provider.
4. Airline philosophy and objectives. Examples exist where airlines of a similar nature (size of fleet, operation, location, market) adopt different organisational approaches. Then it comes down to the airline strategy, the individual character and background of the decision–makers, particularly the Technical Director, and how much control the airline’s management wish to exert over the E&M activities that directly impact the airline.
The most contentious debate is always over maintenance control and line–maintenance. Performance in these areas is so critical to technical dispatch reliability and operational integrity that an in–house model is often adopted. However, if the airline has an outsourcing philosophy and believes in creating true accountability for performance, then these central activities should be part of the outsourced package.
In or out?
The main arguments for having each activity in–house or outsourced are straightforward. Ultimately however, the decision depends on the specific airline and how the factors given above apply.
Heavy airframe maintenance requires large investment in hangars, manpower and tooling. The main decision factor should be size and few airlines have the scale to justify the investment. Despite this, many do — for reasons that are not economic.
In some countries, aircraft maintenance is seen as an important source of employment, technology, skill development and even national pride. The rationale case is that the third–party market is very competitive; aircraft are mobile and if necessary can move to regions where competition exists, and significant scale is necessary to generate the unit costs that outsourcing may provide. The airline has to recognise that even if local labour costs are low (and labour generally represents over 60% of the cost), total cost in terms of turn–time and turn–time reliability must be taken into account.
Component support is management and capital intensive, and again size should be the most important factor. Third–party suppliers who already support large fleets can offer significant economies of scale when it comes to spares provisioning for growth or new aircraft introduction, and when purchasing O&R. Outsourcing the hassle of managing the thousands of different parts required seems a very logical option for small E&M management teams. As a result, outsourcing, flying hour rate contracts and consignment stocks are increasingly common.
Engine overhaul outsourcing decisions tend to be clearer cut because of the costs involved. Just the test cell can put you back $20m. And despite the significant barriers to entry, a contested third–party market does exist (in most engine types though not all) and engines can travel.
As mentioned, line–maintenance is not a clear–cut decision and the most influential factor is often the background, philosophy and experience of the Technical Director. The most important argument for in–house capability is the function’s criticality to operational reliability. Since this is the most visible performance measure that the Technical Director will be made accountable for, on a daily basis, then line–maintenance often ends up in–house.
The strongest case for outsourcing this activity comes when a third–party supplier with scale exists at the operating base. Then the following should be on offer: lower unit costs, a hangar for A checks/casualties/overnight work, and better on–site spares access. And with todays severe shortage of licensed engineers, the supplier would have appropriate resources already trained and in place. But the service provided has to be excellent. The cost of excessive technical delays will rapidly outweigh any unit cost advantage gained.
Technical management is the "intelligence" centre of E&M activity. It is essential for: evaluating new aircraft; developing modifications protecting the asset value of the fleet; tailoring maintenance programmes to the airline’s flight operations, and building reliability analysis and on–condition monitoring into work package design to increase aircraft availability and reduce material/labour costs. To conduct all this work in–house requires investment in and management of a maintenance IT system.
In this case, the "start–point" is probably the most influential factor. An airline with a system and the staff in place is unlikely to suddenly outsource this management activity.
Outsourcing the entire E&M activity would be a radical decision for airlines with some or most of the above activities already in–house. An organisation migration path from profit centre to subsidiary to true third–party would most likely be followed. For an airline that is new or small, then outsourcing is a feasible and logical option.